Subsea bulk oil-water separation (Annual Report 2021-2022)
During the last year we have worked on determining separation characteristics of water and a model oil (Exxsol D60) with small amounts of crude (spiking). This is done to mimic the separation characteristics of real crude-water mixtures in the pipe separator. Rheology properties of the resulting oil-water emulsion were studied under flowing conditions by using a mini-loop. The results of this study suggest that the Pal & Rhodes rheology model with adjusted equation constants is the most suitable to predict the emulsion viscosity in pipe (Fig. 1). Other properties like separation time and inversion point were also studied.
Our first test campaign was focused on measuring drainage potential curves for a single tapping point in the pipe separator with spiked and un-spiked Exxsol D60 and comparison against a simple numerical model. The drainage potential gives a relationship between the water cut of a stream tapped from the bottom of the pipe versus the water flow rate tapped. This work showed that the main factor affecting the shape of the drainage potential curves is the flow pattern of the oil-water mixture approaching the tapping point. Crude oil spiking reduces considerably the drainage potential for oil continuous regimes (low water cuts). (Fig. 2)
The next experimental campaign was focused on measuring the separation efficiency and water cut ratio for spiked oil for various total flowrates and inlet water-cuts. Two different concentrations of crude oil (e.g., 185 and 400 ppm) were used to observe the effect of crude concentration on the separation characteristics. Flow pattern of liquid-liquid mixture in pipe were determined along the separator. Crude oil spiking significantly reduces the efficiency of the pipe separator for oil continuous regimes (low water cuts).
We had technical meetings with experts from Equinor and Sintef to get advice and design our experimental procedures, to present our results and get feedback.
The experimental rig is ready to run experiments with air in 2022.
Fig 1 – Emulsion Rheology Model
Fig 2 – Drainage Potential Curves Study
Subsea bulk oil-water separation (Annual Report 2020-2021)
“To Make more efficient subsea bulk oil-water separation by improving separation design, understanding multiphase flow fundamentals and preventing undesired phenomena during separation process.”:
Green shift impact: Subsea separation of produced water increases the recovery rates for brown field installations. Removing produced water on the seabed increases production rates, removes topside produced water bottlenecks and enables better utilization of existing topside facilities.
1. Background
Management of
produced water is one of the most important issues in production from mature
oil fields. Subsea separation can be used to address this problem and brings
additional benefits. It is therefore important to develop cost-effective subsea
separator technologies, making the business case for subsea separation more
attractive. The benefits of subsea separation can be outlined as three separate
aspects: Subsea separation of produced water can reduce the load on topside
capacity and facilities, allowing for prolonged, increased production and
avoiding bottlenecking. Subsea water separation also reduces the fluid pressure
losses from the seabed to the topside, thus enabling more energy-efficient production.
Finally, separation close to the well means less mixing and agitation, reducing
dispersion formation and allowing for better separation.
This project is a continuation of previous project 2.9, conducted by Håvard Skjefstad. Håvard developed a concept for bulk oil-water separation in pipe, tested it for several operational conditions and studied fundamental phenomena in oil-water separation in pipe.
2. Research activities and deliverables
During the last year
we have worked on how to mimic the separation characteristics of real
crudes-water mixtures by adding small amounts of crude to a model oil (Exxsol
D60). We had technical meetings with experts from Total and Sintef to get
advice and design our experimental procedures.
Water-oil separation bottle tests were performed on the crude oil at
high temperature and for several spiking concentrations at ambient temperature.
Our results indicate that a spiking concentration of 400 ppm has similar
separation characteristics than the original crude-water mixture.
We have also started to run some preliminary tests on the separator prototype.
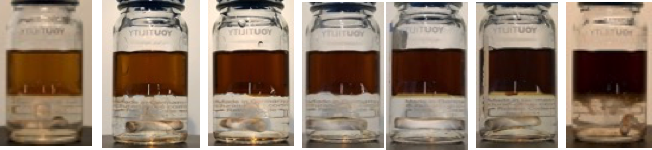
200 ppm 300 ppm 400 ppm 500 ppm 600 ppm 700 ppm 800 ppm |
3. Final Impact
Results of this research can be readily used by the industry to manufacture a new oil-water separator based on our technology or to improve the design of existing oil-water separators on the market. Ultimately, we hope to contribute to improve and facilitate the management of produced water and optimize oil and gas production.
Oil-water bulk separation for oil & gas applications (Short Project Description)
Description:
The benefits of subsea separation can be outlined as three separate aspects. Subsea separation of produced water can reduce the load on topside capacity and facilities, allowing for prolonged, increased production and avoiding bottlenecking. Subsea water separation also reduces the fluid pressure losses from the seabed to the topside, thus enabling more energy-efficient production. Finally, separation close to the well means less mixing and agitation, reducing dispersion formation and allowing for better separation.
A novel concept for subsea oil-water bulk separation has been developed, a prototype of the developed concept has been constructed, and the concept has been evaluated both experimentally and numerically by previous Ph.D. researcher Havard Skjefstad. For experimental testing, a down-scaled prototype of the separator concept has been constructed along with a low-pressure two-phase oil-water test facility. The prototype consists of two 150.6 mm internal diameter pipes in parallel, with a total horizontal length of 6.1 m. Four experimental campaigns have been executed, focusing on performance and operational envelope mapping, design feature evaluation, flow distribution, control strategy development and effect of upstream inlet choking and addition of surfactants. Experimental fluids are Exxsol D60 and distilled water with added NaCl. Separator performance is determined by flow rate, density, temperature and pressure measurements, and pictures of flow phenomena and established inlet droplet distributions are gathered for supplementary analysis.
The prototype exhibits good performance for a wide range of inlet flow rates and water cuts. Based on obtained results, design refinements are suggested and implemented, including preferred location for water extraction and an improved separator inlet configuration. An uneven flow splitting phenomenon is identified for certain flow conditions, which can be detrimental to operability and separator performance.
This project is carried out as a part of SUBPRO, a Research-based Innovation Center within Subsea Production and Processing. This work is financially supported from SUBPRO, which is financed by Research Council of Norway, major industry partners and NTNU.
Constructed and developed prototype showed high potential on multiphase flow separation. Therefore, the main goal is to make more efficient subsea bulk oil-water separation by improving separation design, understanding multiphase flow fundamentals and preventing undesired phenomena. For the next phase of this project following goals are aimed to investigate:
- Experimental study on the effect of small amounts of gas (air) on separation efficiency.
- Experimental study on the effect of effect of surfactants (e.g. crude oil spiking) on the separation efficiency and on the dispersion characteristics with or without inlet choking.
- Experimental and numerical study on the uneven flow splitting phenomenon between branches.
Following topics are considered as additional tentative goals:
- Numerical study of the fluid dynamics in the separator.
- Experimental study on the effect of oil viscosity on separation efficiency.
- Experimental and numerical studies to further refine separator design features.
- Experimental studies to determine optimal control strategies when there is slugging at the separator inlet.
Fig 1. Multi Parallel Pipe Separator (MPPS) prototype